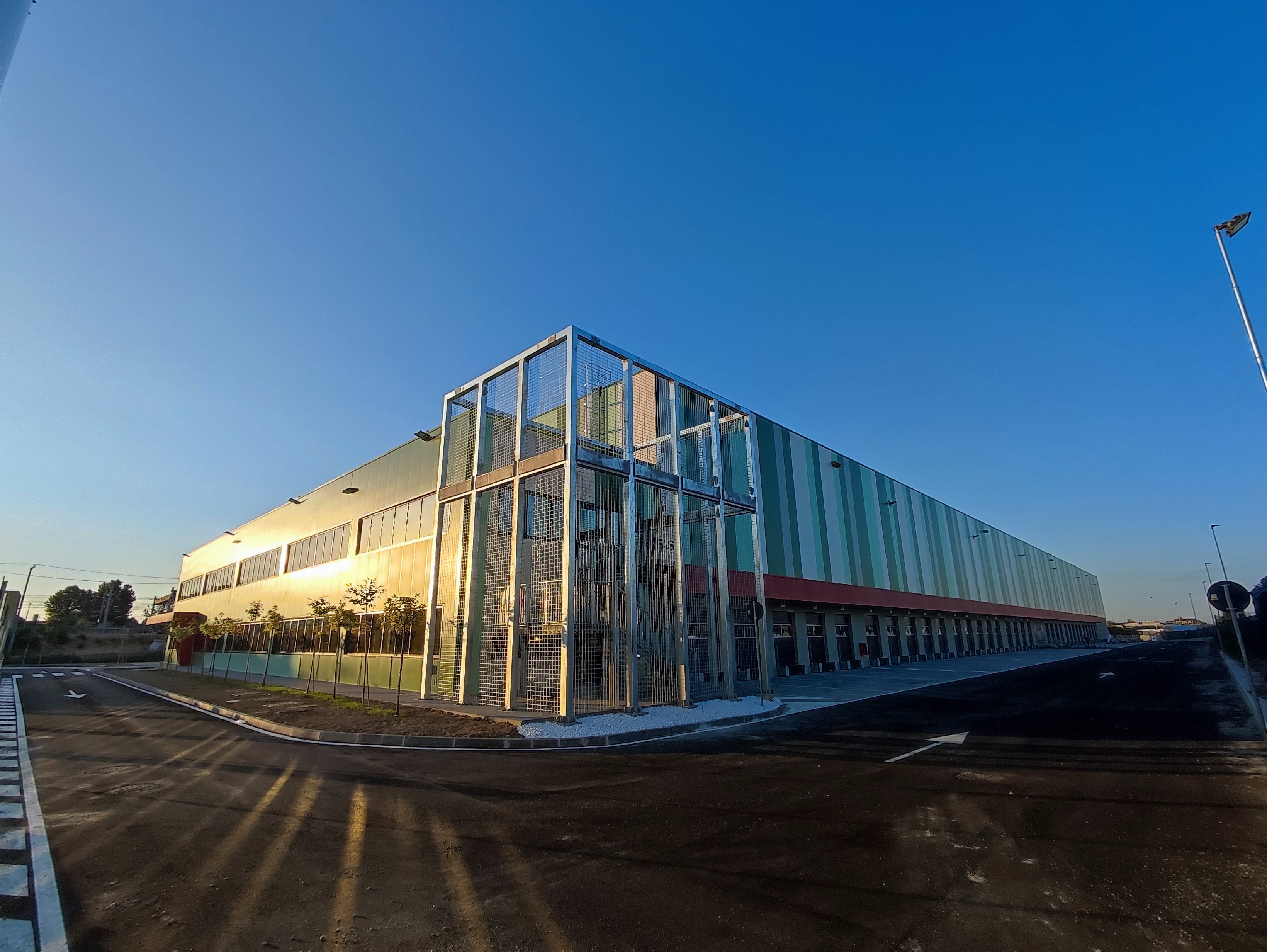
The story of the facility we built at Milan's Ortomercato (wholesale fruit and vegetable market) has become a success case that illustrates our ability to completely rethink projects and adapt them to specific customer requirements, thereby turning a problem into an opportunity.
The construction of our DC3 building is part of the “Foody 2025” initiative promoted by So.Ge.Mi, the company that manages all of Milan’s agri-food markets for the city authorities. The aim of the initiative is to make the Ortomercato a thriving agri-food hub that will attract Italian and international companies and service providers operating in the agri-food supply chain and become a global reference point for the tradition and excellence of the "Made in Italy" label. Our role in the project was to redevelop and regenerate an abandoned area of the market to build a modern and sustainable Class A logistics platform to serve the needs of a few of the companies operating there.
However, after completing the building in the summer of 2022, we realised that the companies based at the Ortomercato had very different needs, characteristics and interrelationships from the large logistics firms we are used to working with, in terms of operating rules, access regulations and land charges . Companies interested in operating in this marketplace are mainly food wholesalers who have synergies within the market itself: entities that need small and medium-sized spaces, and given the agri-food context, spaces with particular features are required. In short, we had built a 10,700 square metre warehouse - with one side for HGV access and the other for small vans and electric vehicles, and around 1,000 square metres of office space on two levels - which did not meet the needs of Ortomercato operators. How did we solve this conundrum?
“We decided to publish a call for tenders for So.Ge.Mi. operators, advertising the spaces that we had available in order to gauge interest and find out more about the operators' requirements, so that any interested companies could express their interest. We decided to have detailed discussions with operators that we already knew to some extent, with the aim of identifying their specific requirements so that we could work out how to adapt the building", explained Rossana Pinato, Operations Construction Manager of Prologis Italia. "The adaptation process was a gradual one. Once we knew which company was going to move in, we worked together on the layout needed". We then arranged for the construction of cold rooms with different temperature ranges suitable for the various food products that would be stored there.
The reconfigured DC3 now houses six operators and is close to being fully leased. The warehouse space has been leased to five customers, with the leased areas varying between 1,300 and 4,050 square metres. The offices have been subdivided into four sections of 130, 140, 250 and 330 square metres, three of which have already been leased (the 250 square metre space is still available).
"This experience of working with food wholesalers has given us experience of a different market from our traditional business. Since we had not built any facilities outside our core sector before, we needed to understand the differences in requirements, regulations and terminology. Once we had worked out what to do, it didn't take long to transform the building", commented Marco Colombo, Vice President, Southern Europe Leasing and Customer Experience Lead at Prologis Italia. "Now we know that when it comes to designing warehouses for the general market, it's better to start with the shell of the building, keeping in mind from the start that it might need to be customised later or divided into small or medium-sized spaces, depending on the specific requirements of each customer. We were able to do this thanks to our strong business flexibility".